Effortlessly Lubricate Your Machinery: Step-by-Step Guide on How to Install Press-In Grease Fittings
Have you ever wondered how to install press-in grease fittings? It’s a task that may seem intimidating at first glance, but with the right tools and steps, it’s actually quite simple. Press-in grease fittings are commonly used in machinery to lubricate hard-to-reach parts, making maintenance easier and extending the lifespan of your equipment. In this blog post, we’ll walk you through the process of installing press-in grease fittings so you can do it with ease and confidence.
Think of it as giving your machinery a much-needed oil change!
Gather Necessary Tools
If you’re planning to install press in grease fittings, there are some tools you’ll need to gather first. The list is short and chances are you may own most of them already, so it shouldn’t take you too long to get everything together. First, you’ll need a drill with the right sized bit to create a hole in the material you’ll be putting the grease fitting into.
A wrench that fits the size of the fitting is necessary to thread it in place. You’ll also need a grease gun to apply the appropriate amount of grease into the fitting. Finally, it’s helpful to have a tap and die set just in case you accidentally strip the threads during installation.
It may seem daunting, but as long as you have these tools and follow the installation instructions carefully, you’ll be able to install the press in grease fittings with ease.
Tools: Grease gun, press-in grease fittings
If you’re planning to perform some maintenance on your machinery, you’ll need to gather a few essential tools first. One of the most crucial tools for lubrication is the grease gun, which allows you to apply grease to hard-to-reach areas easily. A grease gun functions by applying pressure to the grease cartridge, forcing it through the nozzle, and onto the component in need of lubrication.
The press-in grease fittings are the other necessary tool to have. These fittings provide a convenient way to apply grease without over-lubricating the machinery. They’re inserted into the fitting and deploys the right amount of grease by applying friction against the part.
Both of these tools allow you to perform maintenance with ease, reduce downtime, and keep your machinery running efficiently. Don’t forget to add these tools to your maintenance toolbox today.
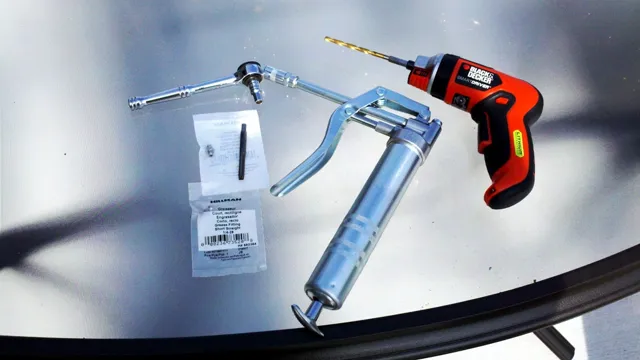
Clean and Prep the Fitting Hole
Before installing press-in grease fittings, it’s crucial to ensure that the fitting hole is clean and prepped properly. The first step is to clean the hole with a degreaser or brake cleaner to remove any dirt, debris or oil residue, which can cause poor fitment and create leakages. Once the hole is clean, it’s important to inspect it for cracks or damage, as a faulty fitting hole can lead to lubricant leakage.
Before installing the fitting, use a tap to clean and remove any remaining debris. This process ensures a secure fit between the new fitting and the hole, which helps ensure the longevity of the fitting and prevents loss of lubricant. By taking the time to clean and prep the fitting hole, you guarantee that your press-in grease fittings will function effectively and efficiently.
Remove old fittings and clean mounting surface.
Before installing any new fittings, it’s essential to remove the old ones and clean the mounting surface thoroughly. This step is crucial to ensure that the new fitting can be installed correctly and securely. If you don’t remove the old fittings, you risk damaging or misaligning the new one, which can lead to leaks and other issues down the line.
To clean the mounting surface, you should use a stiff-bristled brush and a cleaning solution designed for the material you’re working with. For example, if you’re mounting a fitting on a concrete surface, you may want to use a concrete cleaner. Similarly, if you’re working with metal, you’ll want to use a cleaner that won’t corrode the material.
Taking the time to properly prep the fitting hole will make the installation process smoother and ensure that your new fitting functions correctly.
Select the Correct Fitting
When it comes to installing press in grease fittings, selecting the correct fitting is crucial. Ensuring that you have the right size, thread, and style is essential for a perfect fit and a secure connection. The first step is to examine the lubrication points on the machinery or equipment and identify the size and thread of the fitting required.
Next, select a style that is compatible with the equipment, such as a straight or 90-degree angle fitting. It’s essential to choose fittings made of high-quality materials that can withstand high-pressure loads and harsh environments. Finally, use a thread sealant to prevent leaks and ensure a tight seal.
A little bit of planning and the correct fitting can save you time and money in the long run, and keep your equipment running smoothly. Remember to follow all safety protocols when installing fittings and seek professional guidance if you’re unsure.
Choose the fitting that matches the hole size.
Choosing the right fitting for your project can make all the difference in ensuring a successful outcome. One important factor to consider when selecting a fitting is the hole size that it will be inserted into. It is crucial to choose a fitting that matches the hole size to ensure a secure and tight fit.
To determine the proper fitting size for your project, start by measuring the hole diameter accurately. This measurement will help you identify the correct fitting size that will work best for your project. Once you have the measurement, you can then begin your search for the right fitting.
Matching the correct fitting to the hole size is an easy task, but often overlooked. However, choosing a fitting that is too big or too small can lead to fitting failure and issues with your project. This can have disastrous consequences, resulting in safety hazards, leaks, and even damage to your equipment.
Therefore, always take the time to choose the right fitting size for your project. Don’t rush the process or guess at the size of your fitting, as mistakes can be costly. Remember, a proper and secure fit will ensure that your project runs smoothly and the outcome is successful.
In conclusion, selecting the correct fitting size is a critical factor in any project. By taking accurate measurements and matching the fitting to the hole size, you’ll eliminate any guesswork and ensure a safe and secure fit. So, take your time, measure correctly, and choose the fitting that matches the hole size for a successful project outcome.
Press In the Fitting
If you’re wondering how to install press in grease fittings, don’t worry, it’s not as complicated as it sounds. The first step is to clean the fitting and surrounding area of any debris or dirt. Next, you’ll need to line up the fitting with the drilled hole in the part.
Once the fitting is in place, you’ll want to use a press to push the fitting into the hole until it’s flush with the surface. It’s important to make sure that the fitting is straight and not at an angle. If it’s at an angle, it may not provide proper lubrication and could cause damage to the part.
Once the fitting is properly pressed in, you should be able to attach a grease gun and start lubricating the part. Remember, it’s important to regularly lubricate your fittings to ensure they continue to function properly and extend the life of your equipment.
Attach the fitting to the grease gun. Push the fitting into the hole. Check that it’s secure.
If you’re planning on greasing your machinery or automotive parts, attaching the fitting to the grease gun is the first step to take. It’s a simple process, but you need to be careful about it. Firstly, ensure that you have the correct fitting for the job.
Match the size of the hole on the part to that of the fitting. Once you have the right fitting, attach it to the grease gun in accordance with the manufacturer’s guidelines. It should be firmly fixed in place, and there should be no wobbling or looseness.
Next, press the fitting into the hole, applying slight pressure. It should slide in easily, without any resistance. If you encounter any resistance, stop pushing, and inspect the hole and fitting for any deformations or blockages.
Ensure that there’s no debris or dust on the fitting, which could cause contamination or clog the hole. Once you press the fitting into the hole, check its security. Give it a slight tug and check if it’s fixed firmly.
If it’s loose, remove the fitting and check for any damages or obstructions before reattaching it. Ensure that you don’t overtighten the fitting, as this could damage your parts and cause leaks. In summary, attaching a fitting to your grease gun and pressing it into the hole is a simple and efficient way of greasing your machinery.
Just make sure you follow the manufacturer’s guidelines, and your fittings are of the right size and are clean and debris-free before fitting them. Remember to check them for looseness and adjust accordingly before using your grease gun.
Test and Monitor
If you’re looking to install press-in grease fittings, the process is actually fairly straightforward. First, you’ll want to ensure that you have the correct size of fittings for your specific application. Once you have the right size, you’ll want to check that the hole you’ll be inserting the fitting into is clean and free of debris.
From there, you can insert the fitting and use a hydraulic press to push it into place. It’s important to make sure that the fitting is properly seated and secure, as any loose fittings can lead to leaks or other issues down the line. Regular testing and monitoring can help you stay on top of any potential problems and ensure that your fittings are working as intended.
With the right tools and a careful installation process, you can successfully install press-in grease fittings and keep your machinery running smoothly.
Grease the fitting to see if there are any leaks. Monitor regularly to ensure proper lubrication.
When it comes to proper lubrication, testing and monitoring the fittings is crucial. To ensure that everything is functioning as it should, it’s important to grease the fitting and see if there are any leaks. This is best done regularly to keep everything running smoothly.
By monitoring the fittings, you can catch any issues before they become major problems. It’s important to remember that proper lubrication is essential for the longevity of your machinery. Neglecting to oil or grease the fittings can cause excessive wear and even damage to your equipment.
Think of it like a car engine – without oil, the engine will quickly overheat and malfunction. In the same way, a lack of proper lubrication can result in machine failure and costly repairs. So take the time to test and monitor your fittings regularly to avoid any potential problems down the line.
Your equipment will thank you for it!
Conclusion
To sum it up, installing press in grease fittings is much like adding a cherry on top of a sundae – it may seem like a small addition, but it can make a big difference in the overall performance and longevity of your machinery. With the right tools and knowledge, the process can be quick and easy, leaving you with a sweet and satisfying result. So go ahead, give it a try and enjoy the smooth, creamy benefits of a well-greased machine!”
FAQs
What are press in grease fittings?
Press in grease fittings, also known as press-in-style or push-in-style fittings, are a type of lubrication fitting that are inserted into a hole and held in place by the pressure of the surrounding material.
How do you install press in grease fittings?
To install a press in grease fitting, simply insert the fitting into a hole in the material and press it in until it is securely held in place. No additional fasteners or tools are required.
What materials are compatible with press in grease fittings?
Press in grease fittings can be used in a variety of materials, including metal, plastic, rubber, and fiberglass. However, it’s important to choose a fitting that is designed for the specific material to ensure a proper and secure fit.
Can press in grease fittings be removed and reused?
Press in grease fittings can be difficult to remove, and attempting to do so can damage the surrounding material. While they technically can be removed and reused, it is generally recommended to replace them with new fittings if they need to be removed for any reason.