Unlocking the Secret to Successfully Expand Rubbers: Your Ultimate Guide!
Want to learn how to expand rubber with ease? Whether you’re a DIY enthusiast or an industrial worker, the process of expanding rubber can seem daunting. However, with the right tools and techniques, it’s actually a straightforward process that can result in precise shapes and sizes. In this how-to guide, we’ll break down the steps involved in expanding rubber and provide tips to help you achieve the best results.
From understanding the properties of rubber to selecting the right expansion technique, we’ve got you covered. So, buckle up and let’s dive into the world of expanding rubber!
Understanding Rubber Expansion
Rubber expansion refers to the process of increasing the size and shape of rubber material. Knowing how to expand rubber properly is essential for those who work with rubber materials, as it can result in a better end-product. One common way to expand rubber is by stretching it.
When rubber is stretched, it elongates and narrows in width, which can be useful for a variety of industry applications. Another way to expand rubber is by heating it. By applying heat to rubber, the molecules are activated, and the rubber becomes softer and more malleable, allowing it to be molded or shaped more easily.
However, it is important to note that excessive heating can cause the rubber to break down and lose its properties. Understanding the proper techniques for expanding rubber can lead to improved quality and versatility in rubber products.
What Causes Rubber to Expand?
Rubber expansion is a natural occurrence that happens when rubber comes in contact with heat or chemicals. This change in shape can be attributed to the rubber’s molecular structure, which is made up of long chains of molecules. Under normal conditions, these chains are coiled up and compact, but when subjected to high temperatures or certain chemicals, they can unwind and stretch out, causing the rubber to expand.
The expansion can cause rubber products to become too large for their intended use, resulting in a loss of function or even failure. To prevent this from happening, manufacturers may use special materials and treatments when producing rubber products to ensure they maintain their shape and size under a variety of conditions. So, the next time you see a rubber product expanding, think about the science behind it and the precautions that are needed to keep it intact.
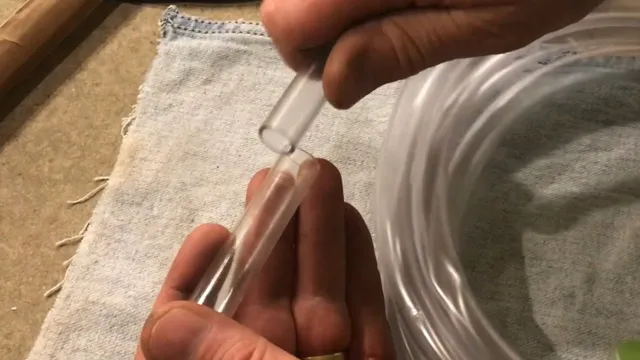
Types of Rubber That Expand
Rubber expansion is a common phenomenon that occurs when rubber is exposed to certain conditions such as heat, moisture, or pressure. Understanding the types of rubber that expand is vital in various industries that use rubber products. One type of rubber that expands is silicone rubber, which is mainly used in high-temperature applications such as cooking utensils, automotive engines, and medical devices.
Another common type of rubber that expands is nitrile rubber, which is used in the manufacturing of O-rings, seals, and gaskets. Additionally, natural rubber, which is primarily used in the production of tires, also tends to expand due to temperature changes. Understanding these types of rubber and their propensity to expand is important in designing and creating precise and reliable products.
Preparing to Expand Rubber
If you’re preparing to expand rubber, it’s important to understand the process and be prepared for any challenges that may arise. To start, you’ll need to determine the type of rubber you’re working with and the specific requirements for expansion. Factors such as temperature, pressure, and moisture levels can all affect the success of the expansion process.
Once you have a clear understanding of the requirements, you’ll need to acquire the necessary equipment and materials, including molds, heating elements, and release agents. It’s also important to establish a safe and efficient workspace, ensuring that all equipment is properly maintained and safety protocols are followed. With careful preparation and attention to detail, you can successfully expand rubber and achieve the desired results.
So, whether you’re expanding rubber for industrial or personal use, take the time to do your research and prepare accordingly to ensure a successful outcome.
Safety Precautions to Take
When it comes to expanding rubber, there are a few safety precautions that you should take to ensure that you don’t get hurt during the process. Firstly, you should always wear protective clothing such as gloves, goggles, and a face mask. This is because the chemicals used in the process can be harmful to your skin and eyes, and can even cause respiratory problems if inhaled.
Secondly, make sure that you have the right tools for the job. This includes rubber molds, a mixing bowl, and a rubber expanding agent. You should also ensure that the area you are working in is well ventilated to prevent any fumes from building up.
Lastly, be sure to follow the instructions carefully and take your time. Rushing the process can result in mistakes, which could result in injury or poor results. By following these safety precautions, you can expand rubber without putting yourself or others in danger.
Equipment Needed for Rubber Expansion
Rubber expansion requires proper equipment to ensure success. To prepare for expanding rubber, you’ll need to gather a few essential tools. Firstly, you’ll need a rubber vulcanization machine to mold the rubber into the desired shape.
This machine will apply heat and pressure to the rubber to promote cross-linking of the rubber molecules. You’ll also need a vacuum chamber to remove any air bubbles that may be trapped inside the rubber. Air bubbles will weaken the rubber and cause it to break when stretched.
Additionally, you’ll need a rubber cutting machine or a pair of scissors to cut the rubber sheet to the desired size and shape. Lastly, you’ll need a mold release agent to make it easier to remove the expanded rubber from the mold once it’s cured. By having all of the necessary equipment before beginning the expansion process, you can ensure that the resulting rubber product will be of high quality, consistent and durable.
Choosing the Right Expansion Technique
Before expanding rubber, it is crucial to choose the right expansion technique to achieve accurate and consistent results. One popular method is chemical expansion utilizing a blowing agent, which creates gas bubbles when activated. Another option is mechanical expansion, often used for thicker rubber pieces to create a cellular structure.
Thermal expansion, where heat is applied to the rubber, is another technique that can be utilized. It’s vital to consider the unique properties and required outcomes of your rubber product to determine the best technique. For example, if you’re looking to maintain flexibility, chemical expansion may be the ideal choice.
On the other hand, thermal expansion may be necessary for thicker rubber pieces that require a more extensive expansion process. By considering the characteristics of your rubber material and the desired results, you can select the right expansion technique effectively.
Techniques for Expanding Rubber
Rubber is a versatile material that can be used in a myriad of applications, but sometimes the rubber needs to be expanded. There are several methods to expand rubber, including mechanical, chemical, and thermal techniques. Mechanical methods involve stretching or compressing the rubber to increase its volume.
On the other hand, chemical methods involve adding a polymer or other chemicals to the rubber to initiate expansion. Lastly, thermal methods involve heating the rubber to allow it to expand. However, it’s essential to note that the type of rubber being expanded will determine the most effective method.
Regardless of the method used, it’s crucial to have precise control over the expansion process to avoid overstretching or damaging the rubber. With the right technique and precision, expanding rubber can enhance its flexibility, durability, and functionality, making it ideal for use in an array of applications.
Heat-Induced Expansion
Rubber expands when exposed to heat, creating the potential for increased production and efficiency in various industries. There are several techniques used to expand rubber, including the use of chemicals or steam to heat the material. One popular method involves using a hydraulic press to compress the rubber at high temperatures, forcing it to expand and take on the desired shape.
Another technique involves the use of a specialized machine that applies heat and pressure to the rubber, causing it to swell and expand rapidly. Regardless of the method used, the key to successfully expanding rubber is to carefully control the temperature and pressure applied, to ensure consistent and accurate results.
Chemical Expansion
When it comes to rubber, expansion is a key factor in many industries. Chemical expansion is one effective technique used to increase the volume and improve the properties of rubber materials. This technique involves the use of chemical blowing agents, which release gases when heated, creating bubbles that expand the rubber.
Chemical expansion techniques include foam extrusion, injection molding, and compression molding. Foam extrusion involves the mixing of rubber with a chemical blowing agent, which is then heated and forced through a die to create a foam product. Injection molding and compression molding involve the use of a closed mold, into which a mixture of rubber and blowing agent is injected or placed, and then heated to expand and form into the desired shape.
Overall, chemical expansion is an essential tool for producing high-quality rubber products with improved properties and performance.
Mechanical Expansion
Mechanical Expansion- Techniques for Expanding Rubber Rubber expansion is essential in various industries to enhance the product’s overall flexibility, durability and resistance towards extreme temperatures and pressures. One of the mechanical ways of rubber expansion is mechanical stretching or vulcanization. Mechanical stretching works by increasing the size of the rubber through mechanical force.
A machine applies pressure to the rubber until it expands and meets the desired outcome. Mechanical stretching is a widely used technique in the tire manufacturing industry, where it helps to enhance tire’s overall strength and longevity. Additionally, another technique for expanding rubber is vulcanization.
In this process, sulfur and other chemicals bring about a reaction, which causes rubber to expand after it is heated. This method is commonly used in making rubber seals and gaskets, as the process forms a more robust and more temperature-resistant product. Thus, rubber expansion techniques play a vital role in the production of high-quality rubber products, and industries should consider these methods while creating their products in the best possible manner.
Tips and Tricks for Effective Rubber Expansion
Expanding rubber may be a tricky task, but with a few tips and tricks, it can be done effectively. One of the best ways to expand rubber is to use heat. Heating the rubber makes it more pliable and easier to stretch.
You can use a heat gun or a hair dryer to warm up the rubber. However, be careful not to overheat the rubber and cause it to melt or become too thin. Another effective way to expand rubber is to use mechanical force.
This can be done by using a stretching machine or by hand. When stretching by hand, begin by stretching the rubber gently and gradually increase the force until you achieve the desired expansion. Another tip for expanding rubber is to use lubricants, such as silicone or oil, to reduce friction during the stretching process.
These tricks, coupled with patience and attention to detail, will ensure you achieve effective rubber expansion.
Conclusion
Expanding rubber is a simple process that involves a bit of heat and a lot of patience. Just like a chef carefully cooking a gourmet meal, you must heat the rubber to its breaking point and then allow it to cool in order to unleash its true potential. Whether you’re expanding rubber to create unique products or simply experimenting with a new hobby, remember that the key to success is to take your time and enjoy the process.
So go forth and expand your rubber horizons with confidence and creativity!”
FAQs
What is rubber expansion joint?
A rubber expansion joint is a flexible connector that is used to prevent damage to pipelines due to thermal expansion and contraction.
What are the benefits of rubber expansion joints?
Rubber expansion joints provide flexibility, absorb noise and vibration, compensate for misalignment, and reduce stress that can lead to pipe failure.
How do you install a rubber expansion joint?
First, clean the pipe surfaces where the joint will be installed. Apply lubricant to the joint, and slide it onto the pipe. Tighten the bolts in a criss-cross pattern to ensure a secure fit.
What are the common materials used in rubber expansion joints?
The most common materials used in rubber expansion joints are neoprene, EPDM, and natural rubber. Each material has unique properties that make it suitable for specific applications.
Can rubber expansion joints handle high pressure?
Yes, rubber expansion joints can be designed to withstand high pressure. The pressure rating of the joint will depend on the specific application and the materials used in its construction.