Unleash the Power of Lubrication: A Step-by-Step Guide on How to Install Drive-Type Grease Fittings
Have you ever noticed that your machinery seems to be running a bit rough lately? It could be time to install drive type grease fittings to ensure proper lubrication. These fittings are designed to deliver grease directly to the moving parts of your equipment, keeping them running smoothly and reducing wear and tear. Installing drive type grease fittings is a simple process that can be done in a matter of minutes.
All you need is a grease gun and the appropriate fittings for your machine. The first step is to identify the location of the fittings and remove any dust or debris that may have accumulated around them. Once you’ve cleared the area, you’ll need to attach the male end of the fitting to the grease gun and slowly inject grease into the fitting.
It’s important to be careful not to overfill the fitting, as this can lead to damage and reduced performance. By installing drive type grease fittings, you can extend the life of your equipment and reduce the risk of costly breakdowns. So the next time you notice a decrease in performance, don’t hesitate to add these fittings to your maintenance checklist.
Your machinery will thank you!
Gather Necessary Tools
Before installing drive type grease fittings, it is essential to gather all the necessary tools. You will need a grease gun, a proper sized wrench, a rag, and of course, the drive type grease fittings. Make sure to choose high-quality grease fittings for lasting performance.
Once you have all the necessary tools, you are ready to start the installation process. It is also important to wear protective gear, such as gloves and eye protection, to avoid any accidents during the installation process. With the right tools and precautions, you can install drive type grease fittings properly and increase the life of your machinery.
Socket wrench set
If you’re planning a DIY project or maintenance task, it’s essential to have the right tools to ensure success. One commonplace tool in any mechanic or handyman’s arsenal is the socket wrench set. A socket wrench set typically consists of a ratcheting wrench handle and various sockets that can fit over nuts and bolts of different sizes.
Gathering the necessary tools before you begin work can save you time and frustration. A socket wrench set is useful for jobs such as tightening bolts, removing spark plugs, or replacing brake calipers. It’s essential to choose the right size of sockets that match the nuts and bolts you’ll be working with to avoid damaging them.
With the proper socket wrench set, you’ll have the confidence to tackle any maintenance project and keep your equipment running smoothly.
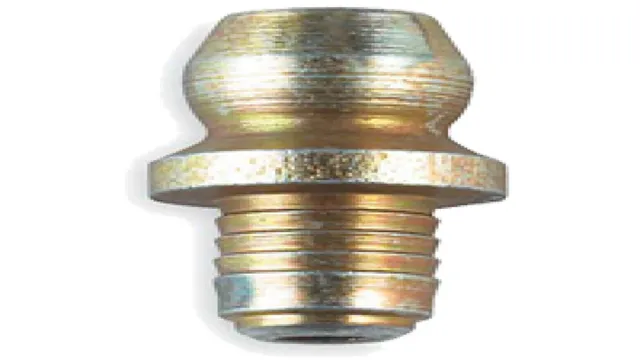
Grease gun
Before you start using a grease gun, it’s important to gather all the necessary tools to ensure a smooth and efficient process. First, you’ll need to select the appropriate type of grease for your equipment or machinery. Make sure to check the manufacturer’s specifications to determine the correct consistency and viscosity of the grease needed.
Next, you’ll need a clean rag or cloth to wipe away any excess grease or dirt before application. It’s also important to have a grease gun, which can be powered manually or through a battery or air compressor. Some grease guns come with adjustable nozzles or extensions to make it easier to reach difficult areas.
Another tool that can be helpful is a grease fitting cleaning tool to remove any buildup that may clog the grease gun. Lastly, don’t forget to wear gloves to protect your hands from the grease. By gathering all the necessary tools beforehand, you’ll be able to complete the task efficiently and avoid any potential mishaps.
Rag or shop towel
If you plan to work on your car yourself, it’s important to gather all the right tools before you start. One essential item is a rag or shop towel. When doing any type of repair or maintenance on your vehicle, there’s bound to be some mess or spills.
Having a rag or shop towel handy will help you quickly and easily clean up any spills or wipe away grease and dirt. When choosing a rag or towel, make sure it’s absorbent and not too abrasive. You don’t want to scratch or damage any surfaces on your vehicle.
It’s also a good idea to have a few extra rags or towels on hand, so you don’t run out in the middle of a job. With a little preparation, you’ll be ready to tackle any repair or maintenance task on your vehicle.
Locate Fitment Points
When it comes to installing drive type grease fittings, the first step is to locate the fitment points. These are the areas on your machinery where the fittings will be inserted to apply the grease. Before you start installation, you need to make sure that you have the correct size fittings for your specific machine.
Once you have the right fittings, you can begin searching for the fitment points. This may require some digging around in the machinery and exploring different areas. Some common places where fitment points can be found include the bearings, joints, and pivots.
Don’t be afraid to get your hands a little dirty and take your time searching for the fitment points – precision is key when it comes to proper installation. Once you’ve located the fitment points, take extra care to ensure that you’re installing the fittings correctly and in the right orientation. A little bit of attention to detail in this process will go a long way in keeping your machinery running smoothly.
Determine correct drive type
Locating fitment points is crucial when determining the correct drive type for your vehicle. Fitment points refer to the areas where the transmission mounts to the engine and the drivetrain connects to the wheels. These points must align correctly with the drive type to ensure proper power delivery and functionality of your vehicle.
A mismatch can result in excessive wear on the transmission and drivetrain, leading to costly repairs. To locate the proper fitment points, refer to your vehicle’s manual or consult with a professional mechanic. Proper fitment will ensure smooth and efficient operation of your vehicle.
Don’t take chances with the wrong drive type, take the time to find the correct fitment points and enjoy worry-free driving.
Refer to manufacturer’s specifications
When it comes to installing aftermarket parts on your car, one of the most important things to keep in mind is to always refer to the manufacturer’s specifications. This is especially true when it comes to locating fitment points. Fitment points are the areas on your car where the aftermarket part will be attached.
These points need to be in the exact same location as the original part to ensure proper fitment and functionality. One of the easiest ways to locate fitment points is to refer to the manufacturer’s specifications. This will usually include diagrams and measurements that will help you locate the exact spots where the part needs to be attached.
By following the manufacturer’s specifications, you can ensure that the aftermarket part will fit seamlessly onto your car and improve its performance without causing any damage or safety issues. So, always take the time to locate fitment points using the manufacturer’s specifications to avoid any potential issues.
Inspect fitment points for damage
When inspecting fitment points for damage, it’s important to first locate them on your vehicle. Fitment points refer to the areas where components are attached or mounted, such as bolts or screws. These points are crucial for ensuring that the parts fit properly and securely, which is essential for maintaining the safety and performance of your vehicle.
Look for damage or wear on the fitment points, such as stripped threads, cracks, or rust. Even minor damage can compromise the strength and stability of the parts, so it’s important to address any issues promptly. By taking the time to properly inspect and maintain your fitment points, you can ensure that your vehicle is in top condition and ready to hit the road safely.
Remove Existing Fittings
If you’re planning on installing new drive type grease fittings, the first step is to remove any existing fittings that are currently in place. This can be accomplished using a variety of tools, including pliers, a wrench, or a specifically designed fitting removal tool. Once you have removed the old fittings, make sure to clean the threads and surrounding area thoroughly to ensure a proper seal when installing the new fittings.
It’s important to note that while it may be tempting to reuse old fittings, it’s always recommended to replace them with new ones to prevent any potential leaks or malfunctions. With the old fittings removed and the area cleaned, you’re now ready to move on to the next step in the installation process.
Clean the fitting area
Before you start installing new fittings, it’s important to remove the existing ones to avoid any potential complications. Start by turning off the water supply and releasing any pressure from the pipes. Once you’ve done that, you can start removing the fittings by gently unscrewing them with a wrench or pliers.
Be careful not to damage the surrounding area or other plumbing components. For rusted or stubborn fittings, you may need to apply some heat with a torch or use a special removal tool. Once you’ve removed the fittings, take the time to clean the fitting area thoroughly.
Remove any debris, grime, or residue that may have accumulated in the area. This will ensure a clean and smooth surface for the new fittings to be installed. Remember to use caution and take your time during this process to avoid any potential accidents or damage to your plumbing system.
By doing this, you can ensure a successful and hassle-free installation of your new fittings.
Use proper size socket wrench
When removing existing fittings, using the proper size socket wrench is crucial for a successful job. The wrong size wrench can not only damage the fitting but also make the job much more difficult than it needs to be. Before starting the removal process, ensure that you have a socket wrench that fits the fitting securely.
If the wrench is too small, it won’t provide enough torque to loosen the fitting, and if it’s too large, it might slip and cause unwanted damage. A quick and easy way to determine the right size wrench is by measuring the nut’s diameter with a caliper or ruler. Remember, having the right tool for the job is essential, so double-check before starting any work.
Turn counterclockwise to remove
When it comes to removing existing fittings, it’s important to first read the instructions carefully to avoid causing any damage to the fixture or surrounding materials. In most cases, fittings are designed to be removed by turning counterclockwise, but this may vary depending on the specific product. Before getting started, it’s important to gather any necessary tools, such as pliers or wrenches, and to ensure that the water or electricity supply is turned off to prevent accidents.
With the right tools and precautions, removing existing fittings should be a straightforward process. By taking your time and following the instructions carefully, you can avoid any unnecessary damage or frustration. Remember, if you’re ever unsure about how to safely remove a fitting, it’s always best to consult a professional for help.
Install New Fittings
If you want to keep your machinery running smoothly, you need to make sure your grease fittings are in good condition. One important aspect is knowing how to install drive type grease fittings. The first step is to select the appropriate fitting and size for your equipment.
Then, clean the area around the fitting before installing it to prevent contamination. Use a wrench or pliers to gently thread the fitting into place, making sure not to cross-thread or over-tighten it. Finally, test your fitting by pumping in some grease and checking for leaks or blockages.
With the right tools and techniques, it’s easy to keep your machinery moving with a properly installed grease fitting.
Apply thread sealant to new fittings
When installing new fittings, it’s crucial to make sure they’re thoroughly sealed to prevent leaks. That’s why you’ll want to apply thread sealant to new fittings before installing them. This will help to create a tight seal that prevents any fluid from escaping or air from entering.
Plus, it will also help to ensure that your fittings don’t come loose over time. Thread sealant works by filling in any gaps or irregularities in the threads to create a tight, secure fit. When applying thread sealant, be sure to use the right amount- too little won’t create a tight seal, while too much can actually cause leaks.
Remember, a little goes a long way when it comes to thread sealant. By taking the time to apply thread sealant correctly, you’ll enjoy a more secure and long-lasting connection.
Thread new fitting into place
If you’re looking to install new fittings, it’s important to know how to thread them into place. One of the most important things to remember is to start with a clean and smooth surface. Make sure the threads are aligned with the fitting and use a thread sealant if necessary.
Tighten the fitting by turning it clockwise until it’s snug. It’s important not to over-tighten, as this can damage the fitting or cause leaks. If you encounter any resistance when turning the fitting, stop and double-check that the threads are properly aligned.
Finally, test the fitting for leaks by running water through it and visually inspecting for any drips or wetness. With these tips in mind, you can successfully install new fittings with confidence.
Tighten using socket wrench
If you’re installing new fittings, it’s important to know how to properly tighten them using a socket wrench. First, make sure the fitting is properly aligned and threaded into the corresponding part. Then, use the socket wrench to tighten the fitting by turning it clockwise.
Be careful not to overtighten it, as that can cause damage or leaks. A good rule of thumb is to tighten the fitting until it’s snug and then give it a quarter turn. Remember to always use the proper size socket for the fitting, as using the wrong size can also cause damage.
By using a socket wrench and following these steps, you can ensure your fittings are properly installed and won’t cause any issues down the line.
Apply Grease
Installing drive type grease fittings is an important step in keeping your machinery running smoothly. Once you have located the proper fitting, use a grease gun to apply the grease. Begin by wiping away any dirt or debris that may have collected on the fitting.
Then, insert the nozzle of the grease gun into the fitting and apply moderate pressure to release the grease. Be sure to watch the grease as it is applied, as this will allow you to gauge how much is needed. Also, be sure not to overfill the fitting, as this can lead to damage.
By following these steps, you can easily and effectively install drive type grease fittings and help your machinery run like new!
Attach grease gun to fitting
When it comes to applying grease, attaching a grease gun to the fitting is the first step. This may seem like a simple task, but it is important to make sure the grease gun is securely attached to the fitting. If it is not attached properly, grease could leak out and cause a messy and potentially dangerous situation.
To attach the grease gun, first, remove the cap from the fitting and wipe the area clean. Then, position the grease gun over the fitting and push it down until it clicks into place. Make sure it is tight enough so that no grease will escape.
Once the grease gun is attached, it’s time to apply the grease. By adding grease regularly, you can maintain the performance and extend the life of the machinery. So, next time you need to apply grease, make sure to follow these simple steps for a smooth and safe process that will keep your equipment running like a well-oiled machine!
Pump grease until it exits the fitting
When it comes to machinery maintenance, ensuring that the moving parts are well lubricated is crucial. One way to achieve this is by applying grease to the fittings. To apply grease, you’ll first need to locate the grease fitting on the machine.
Once you’ve found it, clean the fitting with a rag to remove any dirt or debris that may be present. Next, insert the nozzle of the grease gun onto the fitting and begin pumping the grease into the fitting. You’ll know when the fitting is adequately lubricated when grease starts to come out of the fitting.
Continue to pump until the grease flows consistently out of the fitting. This will ensure that all of the moving parts inside are well lubricated and protected from wear and tear. Remember to use the correct type of grease recommended by the manufacturer, and always follow the recommended maintenance schedule.
Keeping your machinery properly lubricated will help ensure optimal performance, prolong the lifespan of your equipment, and save you time and money in the long run.
Clean any excess grease with rag or shop towel
When it comes to applying grease to machinery or equipment, it’s important to make sure that you’re working with a clean surface. Before you apply any grease, take a moment to clean off any excess grease that may have accumulated. You can use a rag or shop towel to wipe down the surface and remove any unwanted build-up.
This allows the new grease to adhere more effectively and ensures that the machinery will be well lubricated. Once your surface is clean, apply the new grease in a consistent and even manner. By taking the time to prepare your machinery properly, you can extend the life of your equipment and prevent unnecessary wear and tear.
So go ahead and get started by wiping down any excess grease and then applying a fresh layer of lubrication. Your machinery will thank you for it!
Conclusion
In conclusion, installing drive type grease fittings may seem daunting at first, but with the right tools and technique, you’ll be able to tackle the job with ease. Remember to clean the area beforehand and use the appropriate size and thread type for your fittings. And don’t forget to add a little bit of grease to lubricate the process, just like adding some humor to lighten the mood.
With these tips in mind, you’ll be injecting grease like a pro in no time!”
FAQs
What is a drive type grease fitting?
A drive type grease fitting is a type of grease fitting that requires a special tool to install and remove the fitting.
What type of tool is needed to install drive type grease fittings?
A drive type grease fitting requires a special drive fitting tool to install or remove it. This tool fits securely onto the fitting’s head and allows for easy installation and removal.
Can I use a standard grease gun to lubricate drive type grease fittings?
No, a standard grease gun will not work with drive type grease fittings. A special drive fitting tool is required to properly lubricate these fittings.
Can drive type grease fittings be installed on all types of machinery?
Drive type grease fittings may not be suitable for all types of machinery. For example, some high-speed equipment may require a different type of fitting to provide adequate lubrication without causing damage. It is important to consult with the equipment manufacturer or a qualified lubrication professional to determine the appropriate grease fitting for your specific application.