Expert Guide: Effortlessly Change Your Flywheel in Few Simple Steps
If you own a vehicle with a manual transmission, you may have heard of the flywheel. It’s a vital component in the engine that ensures a smooth transfer of power between the engine and the transmission. However, over time, the flywheel can wear down and cause issues with the clutch and gears.
This is where changing your flywheel comes in, and it’s important to do it right. In this step-by-step guide, we’ll walk you through the process of changing your flywheel so you can ensure a smooth drive and a reliable vehicle. So, grab your tools and let’s get started!
Preparation
Changing a flywheel can be a daunting task, but with the right preparation, it doesn’t have to be. First, you’ll need to gather all the necessary tools and equipment, such as a socket set, torque wrench, and jack stands. It’s also important to have a service manual for your specific make and model of vehicle, as it will provide step-by-step instructions and diagrams to guide you through the process.
Before starting any work, make sure the engine and transmission are cool and disconnect the battery to avoid any electrical shocks. You’ll also want to clean the work area thoroughly and have ample room to maneuver underneath the vehicle. Once you feel adequately prepared, you can begin the process of changing the flywheel.
Remember to take your time and follow the instructions carefully to ensure a successful outcome. By taking the necessary precautions and being diligent in your preparation, changing a flywheel can be a manageable task that will greatly improve the performance of your vehicle.
Gather Necessary Tools
When planning a project, it’s crucial to gather the necessary tools beforehand to ensure a smooth and successful process. Nobody wants to start a task only to realize halfway through that they’re missing an essential tool. Gathering the necessary tools minimizes the chances of any inconveniences or setbacks occurring, resulting in a more efficient and less stressful project.
To begin, identify the materials needed and check their availability. This will make it easier to plan for any purchases necessary for the project. Considering the size and complexity of the project, consider whether you need to borrow, buy, or rent any tools.
It’s important to have a complete list of tools and materials before starting the project to get organized and reduce the chances of leaving out any crucial components. By preparing correctly, you can make the project less stressful and more enjoyable.
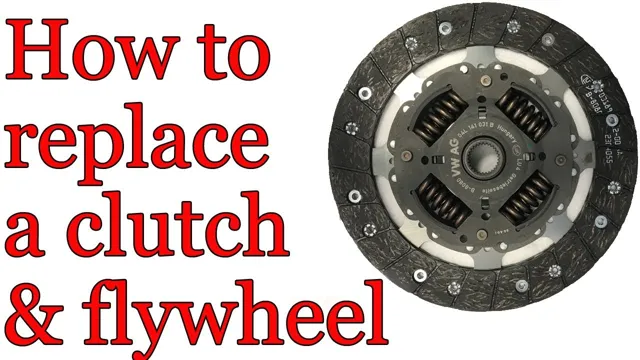
Disconnect Battery
Before disconnecting your car’s battery, it’s important to prepare and take the necessary precautions. First, make sure you have all the tools you’ll need, including gloves and safety glasses to protect your hands and eyes. Always wear closed-toe shoes as well.
It’s also crucial to have the correct size wrench or socket to loosen the battery cables. Once you have your tools ready, locate the battery and make sure the car is turned off with the key removed. Double-check that the parking brake is engaged and the vehicle is in park.
Then, disconnect the negative cable first by loosening the clamp and pulling it away from the battery. Be sure to wrap the cable end in a non-conductive material, such as a rag, to prevent accidental contact. Repeat the process with the positive cable.
Remember, safety comes first when working with car batteries. Taking the time to prepare properly can help prevent injury and ensure a successful battery disconnect.
Removing the Old Flywheel
If you’re wondering how to change a flywheel, the first step is to remove the old one. Start by disconnecting the negative terminal on the battery to avoid any electrical mishaps. Next, you’ll need to remove the transmission, which can be a time-consuming process that involves detaching the clutch assembly and driveshafts.
Once you’ve successfully removed the transmission, you can access the flywheel bolts and unscrew them using a socket wrench. After removing the bolts, you should be able to carefully pry off the old flywheel. Be sure to inspect the old flywheel for any signs of wear or damage before replacing it with a new one.
Changing a flywheel can be a challenging task, so it’s always a good idea to consult a professional if you’re unsure about any of the steps involved. With the right tools and a bit of patience, however, you can successfully change a flywheel and improve the performance of your vehicle.
Remove Transmission and Clutch
Removing the old flywheel is a crucial step when it comes to removing the transmission and clutch. The flywheel must be removed carefully and correctly to ensure a smooth and successful installation of the new one. Before removing the flywheel, it’s important to disconnect the battery so that the engine doesn’t accidentally start: causing potential danger.
Once the battery is disconnected, remove the clutch cover plate and pressure plate to access the flywheel. The flywheel is bolted to the engine block with a series of bolts, which must be carefully removed. The use of a torque wrench is highly recommended, as over-tightening during reinstallation can damage the flywheel or the engine block.
Remove the bolts in a star pattern to prevent warping of the flywheel. After the bolts are removed, the flywheel should come off easily. Inspect the old flywheel for any signs of damage or uneven wear, as this could affect the performance of the new clutch and flywheel.
By carefully following these steps, you can remove the old flywheel without any issues, ensuring a successful installation of the new one.
Inspect for Damage
When it comes to removing an old flywheel, it’s important to inspect it for damage beforehand. Some signs of damage may include wear and tear, cracks, or chipping. This can affect the performance of your engine if left untreated.
Additionally, inspect the flywheel for grease and debris buildup, as this can cause the flywheel to become unbalanced and potentially damage other engine components. Before removing the flywheel, ensure that the engine is in neutral and the spark plugs have been disconnected. Using a flywheel puller, gently remove the old flywheel and inspect it again for any further damage or wear.
If necessary, replace the flywheel with a new one to maintain the proper performance of your engine. Remember to always take caution and follow proper safety protocols when working with engine components.
Mark the Old Flywheel
If you’re replacing the flywheel on your vehicle, it’s important to properly mark the old flywheel before removing it. This will prevent installation errors and ensure that the new flywheel is properly aligned. To do this, use a punch or marker to leave a small mark on the old flywheel and the corresponding spot on the engine block.
This will help you align the new flywheel and ensure that it performs properly. Once you’ve marked the old flywheel, you can remove it using a wrench and socket. Make sure to follow the manufacturer’s instructions and take safety precautions when working on your vehicle.
By marking the old flywheel before removal, you’ll make the installation of the new one much easier and avoid potential complications down the road.
Remove Flywheel Bolts
If you’re looking to remove the old flywheel from your car, the first step is to remove the flywheel bolts. This step may seem simple, but it’s essential to follow the proper procedures to ensure that everything is removed correctly. Start by using a torque wrench to loosen and remove each bolt, being careful not to strip the head.
Before you start, make sure that you have the proper tools, including the correct size socket and wrench. Additionally, it’s crucial to make sure that the engine is at top dead center and that you have a secure and stable workspace. Remember, safety is always the priority, so make sure to wear the right protective gear, including work gloves and safety glasses.
Once the bolts are removed, the old flywheel should come off easily, and you’ll be ready to install the new one. With the right tools and attention to detail, removing the old flywheel will be a breeze.
Remove Old Flywheel
When it comes to removing the old flywheel, there are several steps you need to follow. First, disconnect the battery to avoid any accidents. Then, remove the starter motor and transmission so that you can access the flywheel.
Once you have access to the flywheel, remove the bolts and nuts that hold it in place. It is important to note that some flywheels have clockwise threads while others have counter-clockwise threads, so be sure to check the manufacturer’s instructions. Once you have removed the old flywheel, make sure to inspect it for any damage or wear and tear.
If it is still in good condition, you can reuse it, but if it is damaged, you will need to purchase a new one. Remember to always follow safety precautions when working on your vehicle, and if you are unsure about anything, consult a professional mechanic. By following these steps, you can easily remove your old flywheel and replace it with a new one, ensuring that your vehicle runs smoothly and efficiently.
Installing the New Flywheel
If you’re looking to change your flywheel, then you’re in the right place! Installing a new flywheel may seem daunting, but it’s actually pretty straightforward. Here’s what you need to do. First, locate the flywheel you want to change.
You’ll need to remove the old one first, so make sure you have the right tools on hand. Once you’ve removed the old flywheel, carefully install the new one in its place. Make sure it’s securely fitted before tightening any bolts or screws.
Remember to double check everything before you start the engine to ensure everything is functioning properly. Changing a flywheel can be a time consuming process, but it’s worth it to maintain the longevity and efficiency of your engine.
Clean the Crankshaft
To install a new flywheel, it’s crucial to clean the crankshaft properly. The existing flywheel must be removed from the crankshaft, and the area must be thoroughly cleaned before installing the new flywheel. Any debris, rust, or grime should be removed using an appropriate cleaning solution and a wire brush.
This is important because a dirty crankshaft can result in an imbalanced flywheel, causing vibrations, and affecting the overall performance of the engine. By removing the old flywheel and cleaning the crankshaft, you can ensure that the new flywheel will be perfectly aligned, and that your engine will run smoothly. Remember to inspect the crankshaft before installation and make sure there is no damage or cracks.
With a clean, functioning crankshaft and new flywheel, your engine should be ready to go!
Align New Flywheel
Installing a new flywheel can be a tricky task, but it’s a necessary one when you need extra horsepower from your engine. Aligning the new flywheel is a critical step in the installation process because it helps ensure proper balance and smooth operation. To align the flywheel, make sure the surface is clean and free of debris.
Position the new flywheel on the crankshaft, lining up the bolt holes with the threaded holes on the crank. Then, use a torque wrench to tighten the bolts to the manufacturer’s recommended torque specifications. It’s important to be precise when tightening the bolts, as an unbalanced flywheel can cause serious damage to your engine.
With the new flywheel properly aligned and secured, your engine will be ready to perform at its best.
Install and Tighten Bolts
When it comes to installing a new flywheel, it’s important to make sure the bolts are not only installed, but tightened properly to ensure optimal performance. To begin, it’s crucial to clean the bolts and the mounting surface before installation. Once clean, the flywheel can be placed into position and the bolts can be hand-tightened to hold it in place.
From there, it’s important to use a torque wrench to tighten the bolts to the manufacturer’s recommended torque setting. This will ensure that the bolts are tightened to the appropriate level without being over-tightened, which can cause damage. When tightening, it’s important to tighten the bolts in a cross pattern to ensure even distribution of the force and avoid warping the flywheel.
Overall, proper installation and tightening of the bolts will help ensure a well-functioning and long-lasting flywheel that performs optimally.
Reconnecting Transmission and Clutch
If you’re experiencing issues with your transmission and clutch, it might be time to change your flywheel. The flywheel is an essential component of your vehicle’s transmission system, connecting the engine to the clutch. Reconnecting the transmission and clutch can be an arduous task, but with the right tools and techniques, it can be accomplished.
Firstly, disconnect the battery and remove the transmission. Then, remove the old flywheel and replace it with the new one, ensuring it is mounted correctly. Finally, reassemble the transmission and clutch, reconnect the battery, and test the vehicle for functionality.
Changing a flywheel requires precision and attention to detail, so it is advisable to seek professional help if you are unsure about the process. Nonetheless, if done correctly, changing a flywheel can greatly improve the performance of your vehicle, ensuring a smoother ride and responsive acceleration.
Reattach Clutch and Transmission
Once you have completed the necessary repairs, it’s time to reattach your transmission and clutch. This process is crucial to the proper functioning of your vehicle, so take your time to make sure everything is aligned properly. First, you will need to clean the input shaft and splines on the transmission using sandpaper or a wire brush.
Then, align the clutch disc with the transmission’s splines, making sure it’s properly seated. Once that’s done, carefully insert the transmission onto the engine, making sure everything is aligned correctly. It may take a bit of maneuvering, but be patient and take your time.
Once everything is aligned, torque the bolts to the manufacturer’s specifications. With the transmission bolted in place, it’s time to reattach the starter, driveshaft, and crossmember. After all these steps are completed, start your vehicle and engage the clutch to make sure everything is working smoothly.
Don’t forget to test drive your car to ensure that it’s shifting gears correctly and there are no unusual noises. With this process completed, you can rest assured that your vehicle’s clutch and transmission are in top shape and ready for your daily commute or next road trip.
Reconnect Battery
When it comes to reconnecting the transmission and clutch after working on your vehicle, there are a few things to keep in mind. First and foremost, ensure that the battery is reconnected before attempting to start the engine. It’s important to follow the manufacturer’s instructions for reconnecting the battery while also being mindful of any safety precautions.
Once the battery is reconnected, it’s time to focus on the transmission and clutch. Make sure everything is properly aligned and securely fastened before attempting to operate the vehicle. It’s important to take your time and double-check all connections to avoid any potential issues down the road.
Remember, taking the time to properly reconnect the transmission and clutch can make all the difference in the performance and safety of your vehicle. So, don’t rush through this step and be sure to seek professional assistance if needed.
Test Run and Final Check
Changing a flywheel can be a daunting task, but with the right knowledge and tools, it is certainly doable. Before starting, it is important to lift the car and secure it with jack stands, as the flywheel is located on the bottom of the vehicle. Once it is safely secured, remove the transmission and clutch assembly to expose the flywheel.
Using a socket wrench, remove the bolts holding the flywheel in place and then take out the old flywheel. Before installing the new flywheel, it is important to ensure that it is compatible with the transmission and clutch assembly. Next, install the new flywheel and tighten the bolts to the manufacturer’s recommended torque specifications.
After completing the installation, it is crucial to perform a test run to ensure that the flywheel is functioning correctly. Start the engine and listen for any unusual sounds or vibrations. If everything sounds and feels normal, congratulations – you have successfully changed your flywheel!
Test Flywheel Function
In order to ensure smooth and reliable operation, it’s essential to test the flywheel function of your equipment before its final use. One of the most effective ways to do this is to run a test flywheel function, which allows you to observe the behavior of the flywheel under different conditions. During the test, you can check for any odd sounds or vibrations that could indicate an issue with the flywheel, and adjust the settings accordingly.
This helps to prevent any unexpected problems from arising during use, and gives you peace of mind that your equipment is performing as it should. By conducting a test run and final check of your flywheel function, you’ll be able to ensure optimal performance and longevity for your equipment. So, don’t neglect this critical step when preparing your machinery for use!
Ensure Tightness of All Bolts
When it comes to ensuring the safety and functionality of your equipment, it’s crucial to perform a thorough test run and final check. Part of this process involves ensuring the tightness of all bolts. Even the slightest looseness can cause major issues and put you and those around you at risk.
To avoid this, take the time to go through each bolt and ensure they are all tightened to the appropriate torque specifications. It’s important not to rush through this step or to skip over any bolts, as a small mistake can lead to disastrous consequences. Take the time to do it right and you can have peace of mind knowing that your equipment is safe and ready for use.
Inspect for Any Leaks or Loose Connections
Once you’ve completed the necessary repairs and replacements on your HVAC system, it’s time to give everything a final check before you start using it again. You’ll want to do a test run to make sure everything is functioning properly. Turn on your HVAC system and let it run for at least 30 minutes to see if any issues arise.
While it’s running, perform a final inspection for any signs of leaks or loose connections. This is critical since any leaks or loose connections can cause your system to lose efficiency, and ultimately, cost you money in higher energy bills. During the check, make sure you inspect all the components of your HVAC system, including evaporator coils, condenser coils, and the compressor.
Check for any signs of wear and tear, damage, or corrosion. A thorough inspection can help you identify any potential issues before they escalate into major problems. If you do find any leaks or loose connections, be sure to address them immediately, as minor issues can quickly turn into larger ones.
Overall, performing a test run and final check is essential to ensuring your HVAC system is in excellent working condition. With a little bit of preventative maintenance, you can keep your system running efficiently for years to come, keeping your indoor environment comfortable and your utility bills under control.
Conclusion
In conclusion, changing a flywheel might seem daunting at first, but with the right tools and a little bit of know-how, you can get the job done like a pro. Think of it as a puzzle – take your time, follow the instructions, and soon enough the pieces will fall into place. And, if all else fails, remember the wise words of Benjamin Franklin: “Lost time is never found again.
” So, don’t waste any more time – get yourself a new flywheel and enjoy an engine that purrs like a kitten.”
FAQs
What is a flywheel and why is it important in a car?
A flywheel is a mechanical device that stores rotational energy and helps maintain a steady motion in the engine. It is important because it helps balance the engine and reduces vibrations.
When should I consider changing my flywheel?
You should consider changing your flywheel if you notice unusual noises or vibrations from the engine, difficulty shifting gears, or if your clutch is slipping.
How much does it cost to change a flywheel in a car?
The cost of changing a flywheel in a car depends on the make and model of your car and the type of flywheel you need. On average, it can cost anywhere from $500 to $1500.
Can I change my flywheel by myself or should I go to a mechanic?
It is recommended to go to a mechanic who specializes in transmission or engine repairs to change your flywheel. Changing a flywheel involves several complex steps and specialized tools. Attempting to change it by yourself can result in damage to your car or injury.